Technologies
Constructions of Dropstitch
WND Sports produces inflatable boards with the following drop-stitch constructions:
1.Single Layer + Warp-knitting
2.Glued Double Layer + Warp-knitting
3.Double Wall Fusion (MSL) + Warp-knitting
4.Double Wall Fusion (MSL) + Machine-woven
We evaluate them through the following specifications:
Range
Market Positioning
Selling Price
Weight
Pros
Cons
* Selling Price refers to the one of all-round boards between 10’ and 11’
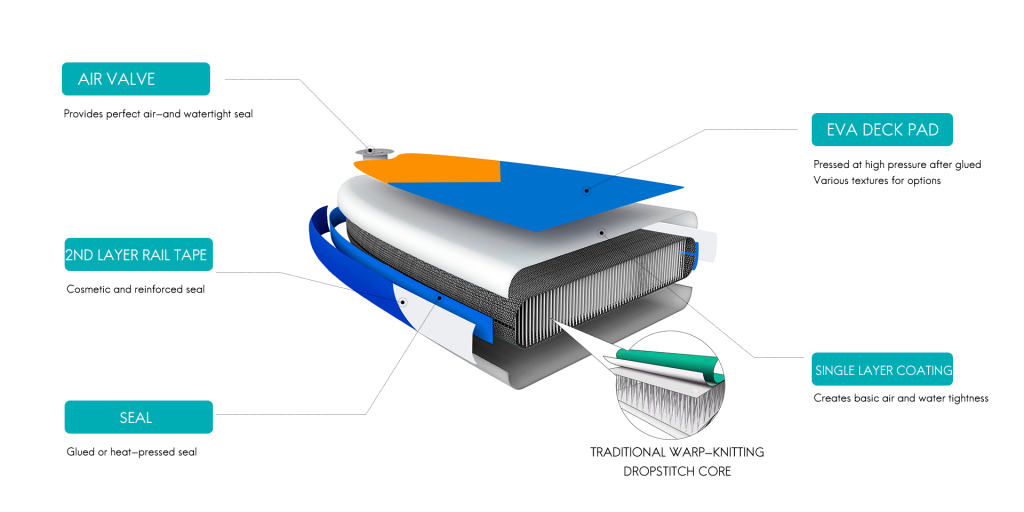
1.Single Layer + Warp-knitting
A thin coating of PVC is laminated on the base cloth of the dropstitch to create airtightness and watertightness. It is currently the most commonly used dropstitch constructions, perfect for budget or low-end boards.
Range
Widely used for all board types except multi-person or team boards
Market Positioning
Usually for low-end market
Selling Price
USD 400 or below
Weight
2550 – 2600 g/sqm
Pros
Good for budget, light weight, perfect for entry-level, friendly to beginners
Cons
Not stiff, rigid or durable enough, not a good choice for a veteran
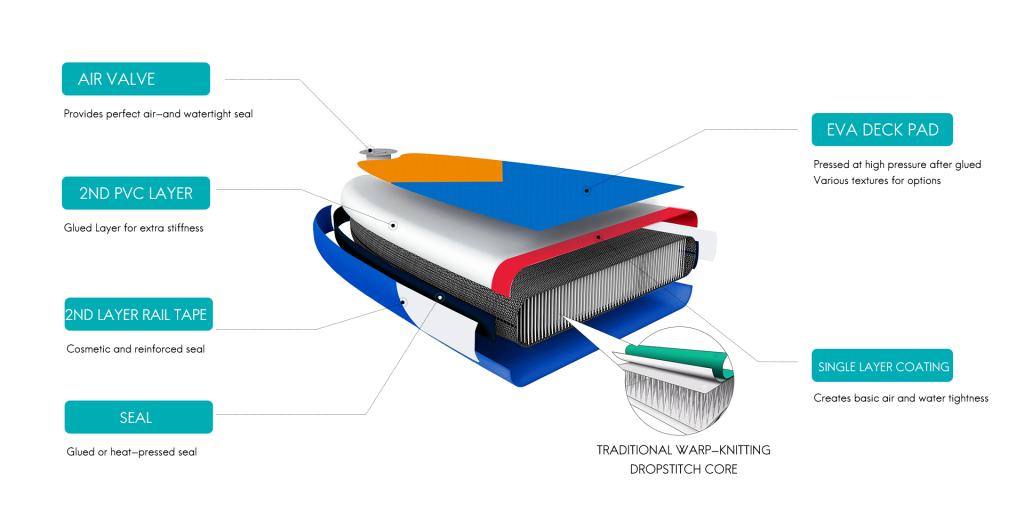
2.Glued Double Layer + Warp-knitting
To create more stiffness while saving cost, an extra PVC layer is laminated to the single layer dropstitch with glue and that is called a glued double layer dropstitch.
Range
Better for multiple-person or team board to provide enough stiffness
Market Positioning
Usually for low or middle-end market
Selling Price
USD 400-800
Weight
3400 – 3500 g/sqm
Pros
Stiffer, more rigid and durable than single layer ones
Cons
20% heavier, 15% more expensive, very hard to roll up, more wrinkles found
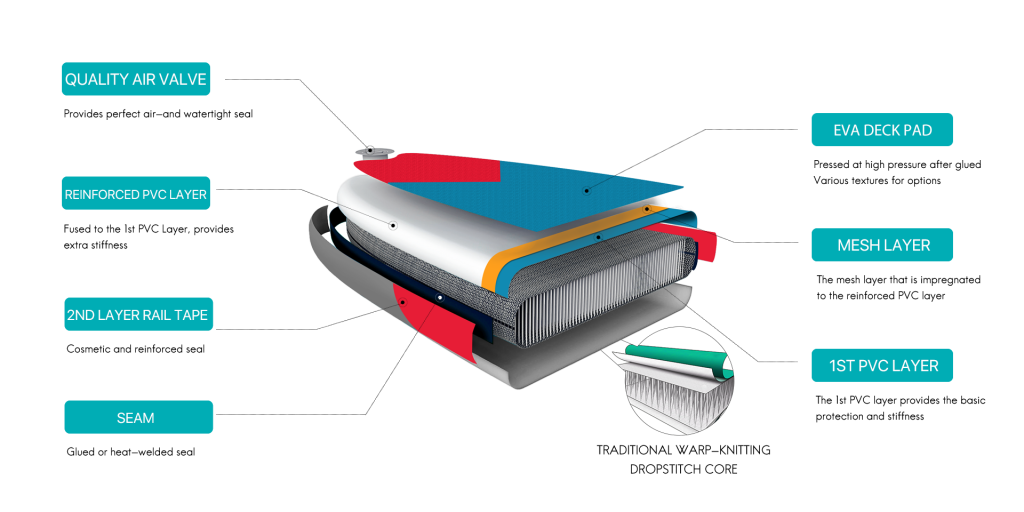
3.Double Wall Fusion (MSL) + Warp-knitting
Double wall fusion is a pre-laminated double layer dropstitch, known as the most advanced tech in the industry. The machine laminate a layer of high-density structural PVC to single layer dropstitch under controlled conditions. It creates a one-shot lamination and glue free construction.
Range
Applicable to all board types and sizes
Market Positioning
Usually for middle-end market
Selling Price
USD 700-900
Weight
3200 – 3300 g/sqm
Pros
Stiffer, more rigid and durable, a good choice for a veteran
Cons
25% heavier, 35% more expensive.
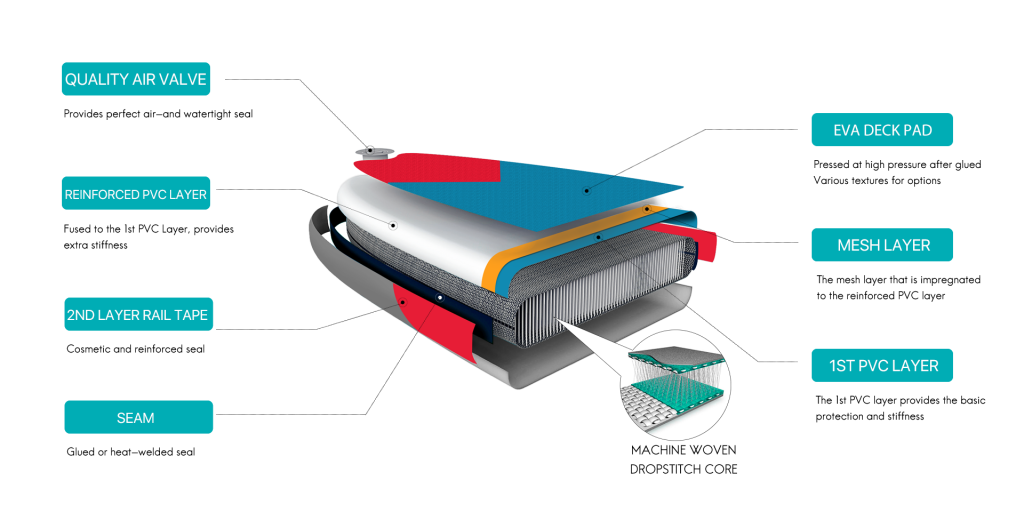
4.Double Wall Fusion (MSL) + Machine-woven
When machine-woven technology meets the double wall fusion (MSL), they create the world’s best dropstitch materials, which inherit all the strengths of the MSL and moreover, become much lighter.
These features make this sort of drop-stitch a most popular material used by high-end brands or products.
Range
Applicable to all board types and sizes and perfect for pro use
Market Positioning
Usually made for high-end and top class market
Selling Price
USD 800 or higher
Weight
2500 – 2600 g/sqm
Pros
Stiffer and lighter, more rigid and durable, perfect for pro users and top brands
Cons
Nothing but expensive
Base Fabric Technologies
Discover the innovation of drop stitch technology, a pivotal element in crafting our inflatable paddle boards and kayaks. Drop stitch involves interweaving thousands of threads between top and bottom layers, forming a robust fabric structure. When inflated, this structure creates remarkable rigidity, allowing our products to glide gracefully on water surfaces. The versatility of drop stitch extends to various water sports, ensuring stability and performance. Experience the pinnacle of strength and lightweight design in our inflatable offerings, all made possible through the ingenuity of drop stitch technology.
There are 2 types of technologies applied to the base fabric of dropstitch core: the warp-knitting and machine-woven.
Warp-knitting
Warp-knitting serves as the predominant base fabric across a comprehensive spectrum of inflatable products. Characterized by a unique thread configuration – one thread at one end and two threads at the other – this versatile technology defines the industry standard. The warp-knitting process offers advantages such as efficient setup and operation, yielding elevated production speed and mitigating raw material expenses. However, it’s essential to note that this methodology may lead to a relatively higher material weight.
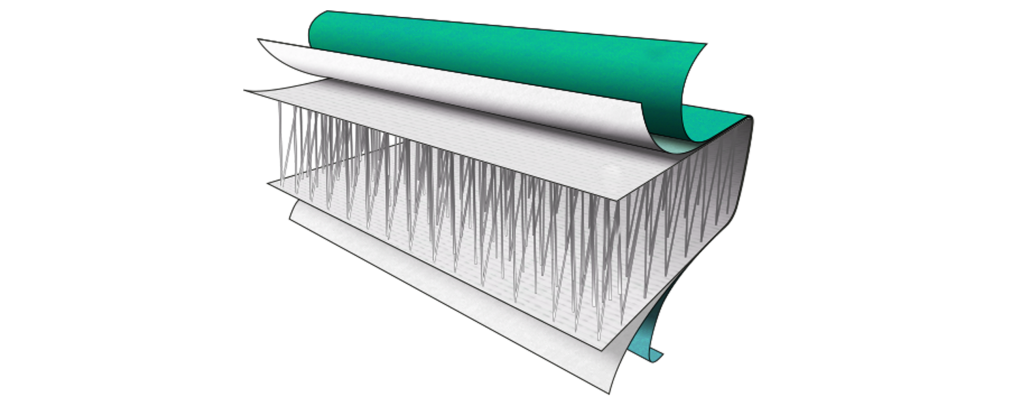
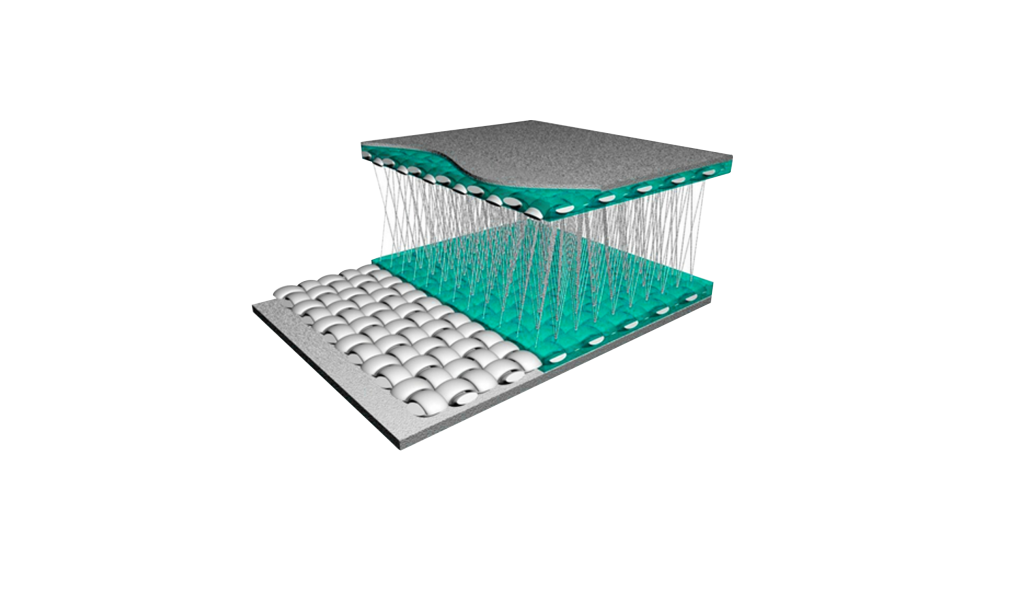
Machine-woven
The utilization of woven base fabric is reserved for high-end inflatable products, renowned for their unparalleled stiffness and performance. Distinguished by a single thread per space yarn, seamlessly interlocking two layers of base fabric, this technique underscores luxurious craftsmanship. It’s noteworthy that the woven base fabric machinery entails a substantial investment, costing 4-5 times more than warp-knitting machines, while also operating at a relatively slower pace. The standout advantage, however, lies in the remarkable 30-40% reduction in weight compared to warp-knitting, enhancing the overall product excellence.